What is Modular?
“Modular” is an offsite construction building technology most effective when done with a high volume of repetition. When we can build numerous similar modules in a factory-controlled process, we can create a high standard of quality and repetition that erects on a job site at mind-blowing speeds without compromise to function or aesthetics. Having tight controls not subjected to the instability of weather through utilizing shop floor production within a controlled environment means no more delays or damaged products due to natural weather conditions. When scheduled right, an entire building can be put together within weeks instead of months, complete with finishes and fixtures ready for occupancy. Working with manufacturers not subjected to areas of higher wage rates also lends the system to cost savings, which is helpful in busy times or over-inflated, high-cost markets.
"You can train people much faster in Modular Construction because they're working on a short set of rote tasks."
– Todd Burns | President of Project and Development Services of the Americas, JLL
Modular Project Examples
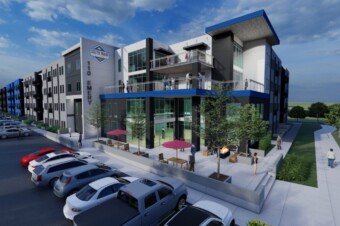
Longmont Multifamily
Longmont Multifamily
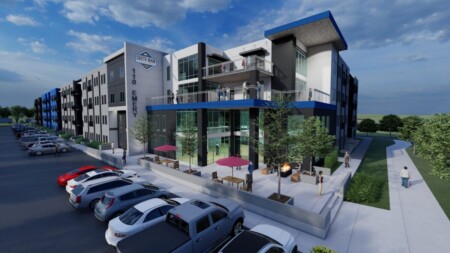
The objective of the Longmont Emery Multifamily feasibility study was to explore the advantages of modular design in addressing Colorado’s ongoing housing shortage. Our EVstudio team assessed a modular solution for a site adjacent to South Main Station in Longmont, with each residential wing of the building designed using modular construction, while the amenity section was designed with traditional stick framing. By integrating innovative modular design with our extensive expertise in multifamily projects, we delivered a comprehensive development study that surpassed our client’s expectations.
Project Link: Click Here
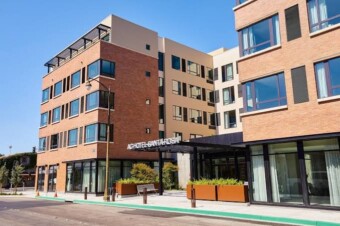
AC Hotel
AC Hotel
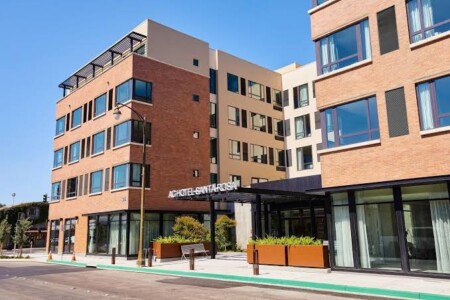
The modular AC Hotel in Santa Rosa California demonstrates the future of efficient, sustainable, and stylish hotel construction. This innovative hotel uses modular building technology to accelerate project timelines, maintain high-quality standards, and reduce environmental impact. Each module, prefabricated offsite, arrived fully equipped with electrical, plumbing, and finishing details. This modular approach reduced on-site construction time, minimizing neighborhood disruption and creating a seamless integration with Santa Rosa’s urban landscape.
The AC Hotel combines modern aesthetics with functionality, showcasing the architectural potential of modular design. Each module reflects Marriott’s contemporary AC Hotels brand, featuring minimalist interiors, sleek furnishings, and spacious layouts. By completing modules in a controlled factory environment, the construction team ensures consistent quality across every room. Consequently, the process also allows for precise energy-saving features, such as high-performance insulation and energy-efficient windows, that align with California’s strict energy standards.
Using modular construction provided key environmental and financial benefits. Offsite production decreased waste, controlled emissions, and optimized material use, supporting Santa Rosa’s sustainability goals. This strategy also enabled faster construction, delivering rooms ready for guests sooner and reducing the impact of rising construction costs. For guests, the modular design provides a comfortable, quiet stay, as factory-assembled walls help insulate sound between rooms.
Located in the heart of Santa Rosa, the AC Hotel offers easy access to local attractions, making it an ideal choice for travelers. The hotel includes a rooftop lounge, fitness center, and high-tech meeting spaces, catering to both leisure and business travelers. Furthermore, it also incorporates California’s indoor-outdoor lifestyle with open-air seating areas and green spaces.
The Santa Rosa AC Hotel is more than a place to stay; it’s an example of sustainable, efficient hospitality design. Through modular construction, the hotel meets high standards of quality, sustainability, and guest satisfaction, showcasing a new era of environmentally-conscious lodging.
Location: Santa Rosa, CA
Modular Manufacturer: Guerdon Modular Buildings
Size: 86 Module / 77,400 SF / 4 Stories / 142 Rooms
Project Link: Click Here
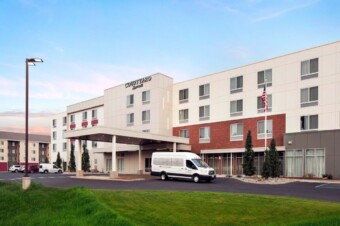
Courtyard by Marriott
Courtyard by Marriott
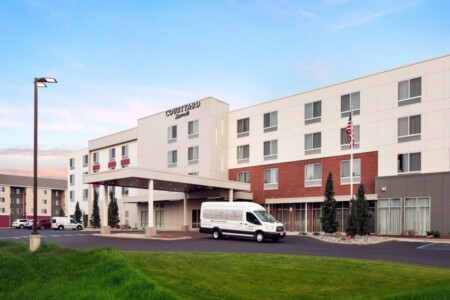
Located at 1255 NE North Fairway Drive in Pullman, this Courtyard by Marriott is on Washington State University’s campus and within one mile of the Palouse Ridge Golf Course. The Pullman Courtyard by Marriott is only the second Marriott hotel to be built using modular construction. The 122-unit hotel was set by crane on the campus of Washington State University in the winter of 2016. On November 16, 2016, a set event where Hoteliers, Developers, and General Contractors witnessed the crane set of Marriott’s second modular hotel to be built using modular technology (first Courtyard brand built using modular technology). The four-story, 76,000-square-foot hotel was built off-site in Boise, ID, with all rooms and finishes in accordance with Marriott specifications. EVstudio Idaho (formerly neUdesign) Architecture provided AOR services for the off-site portion of construction, working closely with the manufacturer throughout the design and construction phases of this groundbreaking project.
Project Link: Click Here
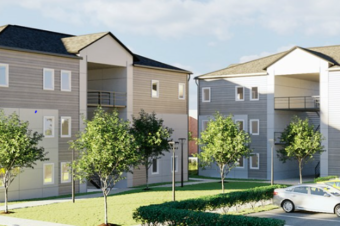
College of Idaho Dorms
College of Idaho Dorms
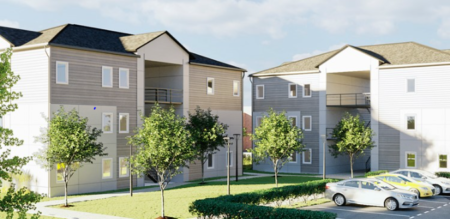
This shipping container-style modular project is a student housing project located at The College of Idaho, Caldwell, Idaho. Site Plans for the dorm include building two three-story structures that will house 27 students each for a total of 54 units of new student housing.
The dorm units were made from repurposed shipping containers and include a common area surrounded by five single dorm rooms. The units are not only durable but sustainable and energy-efficient as well. This is a dynamic project with several local teams including the manufacturer, IndieDwell.
Project Link: Click Here
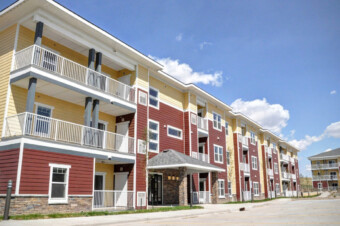
Emerald Ridge
Emerald Ridge
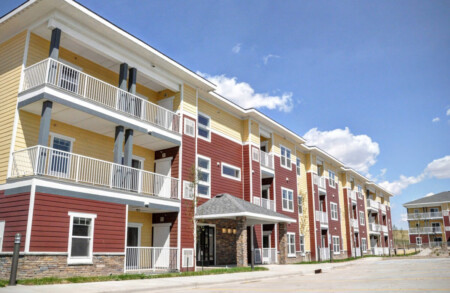
An apartment community in the heart of the North Dakota Oil Boom in 2014 providing long-term housing for oil-field workers and their families. By utilizing modular technology, the construction schedules were condensed and able to provide housing solutions during the unparalleled growth and housing shortage crisis. As most resources were employed by Oil Industries throughout the region, construction resources were extremely limited, further enhancing the efficiency of off-site construction. EVstudio Idaho’s (formerly neUdesign) role as Architect of Record over the Modular Portions of Construction helped bring this project to fruition on an expedited schedule to address the immediate housing needs.
Project Link: Click Here

Spring Creek Apartments
Spring Creek Apartments
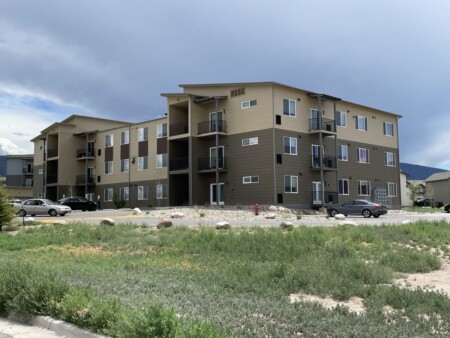
The Spring Creek Apartments project in Gypsum, Colorado, aims to address the critical need for quality, affordable housing in the region while creating a welcoming and vibrant community for its residents. Located near local amenities and transportation options, this project offers residents both accessibility and convenience, enhancing the livability and long-term value of the community.
The project consists of thoughtfully designed apartment units that prioritize efficiency, comfort, and affordability. Each unit maximizes interior space with an open floor plan, incorporating natural light, quality finishes, and energy-efficient appliances. These design choices contribute not only to resident comfort but also to reduced utility costs, providing significant financial savings over time. Additionally, the site features modern community spaces, including green outdoor areas and multi-use gathering spots. These elements encourage a sense of community and provide ample space for recreational and social activities, fostering an inclusive neighborhood atmosphere.
Spring Creek Apartments also demonstrate a commitment to sustainability and eco-friendly design. High-performance materials are utilized throughout construction, prioritizing durability and energy conservation. In keeping with the broader sustainability goals, the project incorporates strategies to minimize its environmental impact, including optimized energy systems and locally sourced, sustainable building materials. By prioritizing sustainable building practices, Spring Creek Apartments reduce their overall carbon footprint and reflect a commitment to environmental stewardship.
This development represents an important step toward addressing the affordable housing shortage in Gypsum, meeting the needs of a diverse and growing population. With a focus on quality, community, and sustainability, Spring Creek Apartments offer residents an affordable, high-quality place to live, while setting a positive example for future developments in the region.
Location: Gypsum, CO
Specs: 10 Buildings / Modular Construction / 3-Story Apartments / 226,000 sf
Modular Manufacturer: Nashua Builders
Apartment Website: Spring Creek Apartments
Project Link: Click Here
Practical, Efficient, Repeatable
Modular construction is a building technology. If you have a product that can lend itself to any sort of regularity and repeat in layout, modular construction should certainly come to the forefront as a potential method of construction for your project. Whether that is multifamily, hospitality, single family attached or detached housing, modular lends itself to be a cost-effective and higher quality product than that of site-built construction.
Not many architecture and engineering firms can say they have deep expertise in modular construction. Not only have we been designing for offsite construction for over a decade, but we have also built a specialized team dedicated exclusively to it over the past several years, known as the EVolution Studio. With clients like Marriott promoting the modular industry, we see this as a serious part of the marketplace that will continue growing. Our staff has not only produced For-Permit Construction drawings, but we have also worked hand in hand utilizing 3D software (Revit and StrucSoft) in partnership with our modular manufacturer network to share and generate shop drawing level production. We know the ins and outs of the industry at a hammer and nail level of detail, knowing that when we design your modular project it will be optimized for modular construction and reap the maximum rewards for your project.
Smooth and Easy Point of Contact
Our team isn’t comprised of just architects and engineers. We are experts working through the technical aspects of planning, simplifying the process with invaluable coordination of on-site feasibility, density, master and community planning, entitlements, and a myriad of other planning services. Our combined proficiencies mitigate lengthy, superfluous efforts in the planning process. We also have an extensive network of manufacturers, experienced General Contractors, Set and Stitch contractors, and everyone else you need for a successful project.
Pioneers in Reversible Design (TM) and Reversible Building (TM)
EVstudio is leading the way in Reversible Design (TM), the proprietary integrated Architecture and Engineering design process that allows the construction of modular buildings that can be deconstructed and relocated – known as Reversible Buildings (TM). Contact EVstudio’s experts today to learn more.
The benefits of modular . . .
- Higher Quality. Modular manufacturing quality is consistently better when compared to site-built construction. Built in a factory setting, the process for all the pieces in under intense quality control.
- Cost Savings. Modular cost can be up to 15% cheaper than stick-built.
- Local Knowledge. Not only do we specialize in the design of modular buildings, but we know how to determine if land is optimal for fostering a particular development program. Through effective due diligence, we'll help you develop a winning pro forma. All modular construction complies with local jurisdiction requirements, including building energy codes.
- Speed of Construction. Modular projects can have as much as a 50% time savings over stick-built. Through construction, EVstudio can also conduct site inspections to ensure all components are built and installed per design in real time, further increasing the speed of execution.
- Design Customization. When the architect understands the guidelines of the engineering that takes place in the factory, there's virtually no limit to the design styles you can build with modular construction. From Traditional to Tudor and Colonial to Contemporary, our modular buildings are not limited to any specific architectural style.
- Minimization of Field Work. The time savings for modular homes primarily comes with the construction/assembly phase. Simultaneous site development and construction in the plant reduces the schedule. Our modular projects are even more affordable and accessible for projects in rural areas. Building in a location that is difficult to get to and far from major population centers have little to no workforce. When nearly every element of a project can be constructed in the factory, the time in the field is reduced incredibly.
Modular Articles

Lean Manufacturing and Offsite Construction
Lean Manufacturing and Its Role in Offsite Construction In today’s competitive construction landscape, efficiency and precision are no longer optional. They are essential. That’s where

SKU Numbers in Lean Manufacturing
The Power of SKU Numbers in Lean Manufacturing and Offsite Construction In modern manufacturing, precision, efficiency, and inventory control are essential. One of the key

Single-Stair Buildings in Colorado
Colorado HB25-1273: Unlocking the Potential of Single-Stair Multifamily Buildings In May 2025, Colorado passed House Bill 25-1273, which allows single-stair multifamily buildings under specific conditions.
Building Futures: EVstudio’s Proud Partnership with Broomfield High School’s Construction Program
Building Futures: EVstudio’s Proud Partnership with Broomfield High School’s Construction Program Empowering Students Through Hands-On Learning EVstudio had the honor of collaborating with Broomfield

Service Offered – MEP Modeling
Collaborative Design with MEP Modeling At EVstudio we approach design as a fully integrated design team. We believe that Architecture is made better when engineering

Project Spotlight – Yellowtail
Yellowtail Duplexes In Big Sky, Montana Welcome to the Yellowtail Duplexes in Big Sky, Montana. This project was developed with Fire Lookout Capital, sitting proudly

Sawtooth Apartments – A Unique Addition to Gunnison County
EVstudio is proud to celebrate the completion of Sawtooth, the second phase of an impactful residential development in Gunnison, Colorado. This new apartment complex builds

EVstudio at World Of Modular 2025: From Presentations to Recognition
This year’s World Of Modular conference brought the modular design community together in Las Vegas, and EVstudio was proud to be right at the heart

The Benefits of an Architecture Firm Holding a Modular Dealer’s License in Colorado
The Benefits of an Architecture Firm Holding a Modular Dealer’s License in Colorado Modular construction continues to gain traction across Colorado as an efficient and

Midland Apartments: A Model for Public-Private Modular Housing in Buena Vista
Midland Apartments: A Model for Public-Private Modular Housing in Buena Vista The Midland Apartments in Buena Vista, Colorado, are a standout example of how innovative
Questions? Ready to get started? Make it happen! Contact our EVolution Studio and let's start the conversation today!
Opening the Playbook on Modular Design
Need example reference documents for your modular project? Below are three pdfs outlined by our EVolution Studio to provide example deliverables for before you get started with us!