Achieve faster Speed to Market with Modular Construction
From simple lodging to luxury hotels, our innovative offsite construction methods meet the hospitality industry’s unique demands. With modular construction, you benefit from reduced labor costs, minimized waste, and the ability to radically shorten the construction schedule and get your project cashflow moving faster with no compromise to function or aesthetics. Our designs incorporate the latest trends in guest comfort and technology, ensuring your property stands out in a competitive market.
“a process in which a building is constructed off-site, under controlled plant conditions, using the same materials and designing to the same codes and standards as conventionally built facilities – but in about half the time.”
– Modular Building Institute
Offsite Hospitality Project Examples
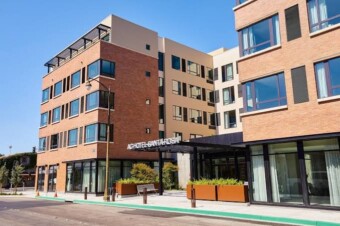
AC Hotel
AC Hotel
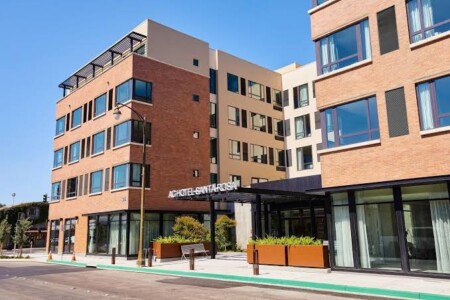
The modular AC Hotel in Santa Rosa California demonstrates the future of efficient, sustainable, and stylish hotel construction. This innovative hotel uses modular building technology to accelerate project timelines, maintain high-quality standards, and reduce environmental impact. Each module, prefabricated offsite, arrived fully equipped with electrical, plumbing, and finishing details. This modular approach reduced on-site construction time, minimizing neighborhood disruption and creating a seamless integration with Santa Rosa’s urban landscape.
The AC Hotel combines modern aesthetics with functionality, showcasing the architectural potential of modular design. Each module reflects Marriott’s contemporary AC Hotels brand, featuring minimalist interiors, sleek furnishings, and spacious layouts. By completing modules in a controlled factory environment, the construction team ensures consistent quality across every room. Consequently, the process also allows for precise energy-saving features, such as high-performance insulation and energy-efficient windows, that align with California’s strict energy standards.
Using modular construction provided key environmental and financial benefits. Offsite production decreased waste, controlled emissions, and optimized material use, supporting Santa Rosa’s sustainability goals. This strategy also enabled faster construction, delivering rooms ready for guests sooner and reducing the impact of rising construction costs. For guests, the modular design provides a comfortable, quiet stay, as factory-assembled walls help insulate sound between rooms.
Located in the heart of Santa Rosa, the AC Hotel offers easy access to local attractions, making it an ideal choice for travelers. The hotel includes a rooftop lounge, fitness center, and high-tech meeting spaces, catering to both leisure and business travelers. Furthermore, it also incorporates California’s indoor-outdoor lifestyle with open-air seating areas and green spaces.
The Santa Rosa AC Hotel is more than a place to stay; it’s an example of sustainable, efficient hospitality design. Through modular construction, the hotel meets high standards of quality, sustainability, and guest satisfaction, showcasing a new era of environmentally-conscious lodging.
Location: Santa Rosa, CA
Modular Manufacturer: Guerdon Modular Buildings
Size: 86 Module / 77,400 SF / 4 Stories / 142 Rooms
Project Link: Click Here
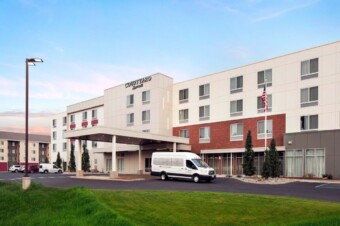
Courtyard by Marriott
Courtyard by Marriott
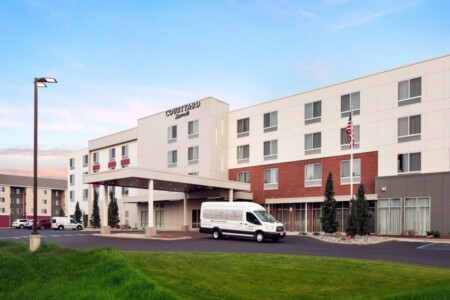
Located at 1255 NE North Fairway Drive in Pullman, this Courtyard by Marriott is on Washington State University’s campus and within one mile of the Palouse Ridge Golf Course. The Pullman Courtyard by Marriott is only the second Marriott hotel to be built using modular construction. The 122-unit hotel was set by crane on the campus of Washington State University in the winter of 2016. On November 16, 2016, a set event where Hoteliers, Developers, and General Contractors witnessed the crane set of Marriott’s second modular hotel to be built using modular technology (first Courtyard brand built using modular technology). The four-story, 76,000-square-foot hotel was built off-site in Boise, ID, with all rooms and finishes in accordance with Marriott specifications. EVstudio Idaho (formerly neUdesign) Architecture provided AOR services for the off-site portion of construction, working closely with the manufacturer throughout the design and construction phases of this groundbreaking project.
Project Link: Click Here
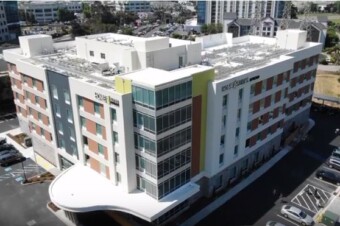
Hilton Home 2 Suites
Hilton Home 2 Suites
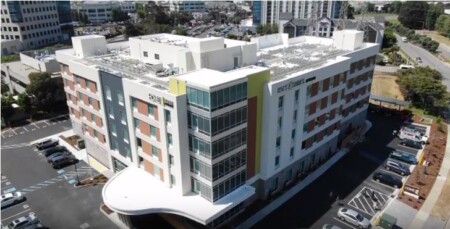
We had the opportunity to partner with a great team to produce the first Modular Hotel in the San Francisco Bay area. As Modular AOR for the Hilton Home2, EVstudio was able to leverage our years of industry experience to help bring the design to fruition. The offsite construction process was able to assist the developer in their goals of expedited delivery in an urban setting, allowing the Hotel to be open 8 months ahead of the traditional build schedule.
The 155-room project was a hybrid design with the ground floor utilizing traditional construction and levels 2-5 utilizing a modular delivery method. We were able to complete the State Permit Submittal package and coordinate the modular portion of the design with the project AOR to ensure proper coordination between the two delivery methods.
Location: San Francisco, CA
Modular AOR
Specs: 144 Rooms / 87 Module Hotel / 4-Stories Modular / 78,300 sf
Project Link: Click Here
The benefits of modular . . .
- Higher Quality. Modular manufacturing quality is consistently better when compared to site-built construction. Built in a factory setting, the process for all the pieces in under intense quality control.
- Cost Savings. Modular cost can be up to 15% cheaper than stick-built.
- Local Knowledge. Not only do we specialize in the design of modular buildings, but we know how to determine if land is optimal for fostering a particular development program. Through effective due diligence, we'll help you develop a winning pro forma. All modular construction complies with local jurisdiction requirements, including building energy codes.
- Speed of Construction. Modular projects can have as much as a 50% time savings over stick-built. Through construction, EVstudio can also conduct site inspections to ensure all components are built and installed per design in real time, further increasing the speed of execution.
- Design Customization. When the architect understands the guidelines of the engineering that takes place in the factory, there's virtually no limit to the design styles you can build with modular construction. From Traditional to Tudor and Colonial to Contemporary, our modular buildings are not limited to any specific architectural style.
- Minimization of Field Work. The time savings for modular homes primarily comes with the construction/assembly phase. Simultaneous site development and construction in the plant reduces the schedule. Our modular projects are even more affordable and accessible for projects in rural areas. Building in a location that is difficult to get to and far from major population centers have little to no workforce. When nearly every element of a project can be constructed in the factory, the time in the field is reduced incredibly.
Questions? Ready to get started? Make it happen! Contact our EVolution Studio and let's start the conversation today!
Opening the Playbook on Modular Design
Need example reference documents for your modular project? Below are three pdfs outlined by our EVolution Studio to provide example deliverables for before you get started with us!