Last month, I discussed the exciting potential of self-healing concrete to reduce global carbon emission and reduce the enormous cost of replacing cracked concrete. Today, I will discuss another innovation to a material that is almost as ubiquitous as concrete, asphalt! None other than the same researches that are innovating self-healing concrete at Delft University of Technology in the Netherlands have come up with a simple solution for doubling the lifespan of asphalt roadways. The ability to deliver a life span twice as long as a normal asphalt road would allow the redirection of some of the $190 billion per year that the United States and Europe spend on highways, streets, and bridges to other infrastructure projects. It would also reduce the amount of greenhouse gases emitted into the atmosphere from the production and placement of asphalt.
Erik Schlangen explains in his TEDx talk, posted to the end of this blog post, the problem they were looking to solve by creating self-healing asphalt. Even though this technology can be applied to normal asphalt surfaces, the Netherlands needed to try to extend the lifespan of their highways which use porous asphalt exclusively. Porous asphalt is used in the Netherlands to reduce the noise pollution from traffic. Strict noise regulations can’t be met with sounds barriers alone, so the porous asphalt is used to absorb the sound into the asphalt itself. Another major benefit of porous asphalt is the ability of water to drain through the surface and into the soil. This largely reduces the need for storm water infrastructure to carry water away from impervious surfaces. However, one downside of porous asphalt is its propensity to ravel.

Asphaltic roads are 90% crushed rock. Normally the aggregate is held together by a bituminous mixture. In porous asphalt, the bituminous binder is used to hold the aggregate together in only key contact point areas. As seen in the photo, due to UV light, oxygen, and weathering over the lifespan the bitumen loses its contact with the stone aggregate. This causes the aggregate to come loose, or ravel.
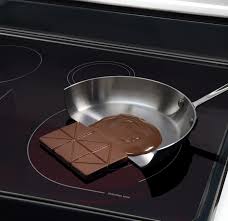
What researchers at Delft University did was mix steel wool strands, the same you would use in your kitchen, into the bitumen mixture. Using induction the steel wool is able to heat up and re-melt the bituminous mixture, effectively re-binding the material back together. Using induction heating is important, because only the metal from the steel wool is heated. This allows the stone aggregate to remain cool, which increases the speed at which the bitumen cools back down and cars can return to driving on the surface.
In a test strip of a highway in the Netherlands they tested out the material in real world conditions. By driving their induction machine over the porous asphalt pavement every 4 years, the researches have estimated that the roadway will have approximately a 30 year lifespan. This measures favorably against normal asphalt surfaces, which have a lifespan of 25-30 years.
Thanks for reading, and once again stay tuned next month for the discussion of another material in my self-healing materials blog post series.