In most projects (excepting single family homes), some fire-rated assemblies will be required. In the United States, most of these assemblies are tested, verified, and documented by Underwriters Laboratories and are identified by an assembly number. UL Design Number U465, for example, identifies a one-hour fire-rated assembly with steel stud framing members of 3 5/8” minimum stud depth. For more information on framing depth and spacing requirements and exceptions: https://evstudio.com/stud-sizes-and-spacing/
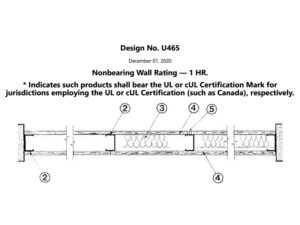
Often, there are multiple listed assemblies that may be used, depending on framing material and client preference. (Preferences may be based on material costs, ease of construction, preference of trusted builders, or material performance over time.) If a contractor is on board early in the design process, or if the client has particular inclinations, it is helpful to discuss cost and construction benefits and implications of UL assembly options before beginning construction documents.
Why is this best chosen early?
Assemblies are rarely a one-to-one or even nearly one-to-one relationship. Seemingly simple things like changing the thickness of the sheathing or the underlayment can have significant impacts on a completed or nearly completed set of construction documents, especially if the architects and engineers are using 3d modeling software. If a changed assembly requires changes in truss depth or sheathing thickness, the floor assembly depth changes. Typically, designers indicate floor to floor heights based on pre-cut stud lengths for ease of construction, cost savings, and to minimize waste, so a change in floor assembly depth results in overall building height change and significant rework by the design team.
Additionally, some building materials are only tested, approved, and listed with certain UL assemblies. If the client or contractor would like to use a specific product, but the drawings were not executed with that in mind and utilizing the assembly where that product is listed, assemblies may need to change in order for the product to be used in the field. Depending on the above (if the product is a different thickness than that originally specified), greater implications to the drawing set and project schedule may exist.
One example of this recently came from a fire damper manufacturer. There are two similar UL assemblies (M508 and L521). One was tested with (and therefore lists) a specific manufacturer’s fire damper. Another manufacturer’s product was tested with and is listed with the other assembly. Those two products may be similar and equitable, but they may not be field substituted, as the contractor is restricted to those manufacturers and products that are listed in the UL assembly’s specific documentation.
Even if the assemblies are very similar, it is not usually a quick and easy process to change assemblies in drawings during or immediately prior to construction. Often, material callouts for rated assemblies are included throughout the construction documents and require thorough revision and review to ensure the change is consistent. The Authority Having Jurisdiction will also need to re-review and approve changes to fire-rated assemblies, which could have associated review fees and review times effecting project schedule.
In addition to fire-rating concerns, certain building types (like townhomes or multi-family housing) will have Sound Transmission Classification (STC) minimums required by the building code. Minimum rating for floor-ceiling and wall assemblies between units in multi-family construction is STC 50 according to the 2018 IBC (Section 1206.2). Many UL listed assemblies will have optional inclusions to meet the required ratings and manufactures often have information on their websites showing how their product can be used in UL assemblies and/or to meet certain STC minimums. For example, USG has a helpful guide:
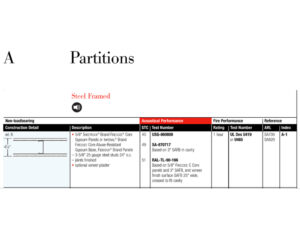
If the client or builder have products they would like to use, that manufacturer’s technical data may be a good place to start. Deliberate decisions on rated assemblies early in the design process helps to ensure the client can use the materials and processes that they prefer and can save rework and review times down the road.
Other related reads:
https://evstudio.com/what-is-the-difference-between-stc-cstc-and-cac/
https://evstudio.com/dwelling-unit-separation-wall-at-duplexes-and-townhomes/
https://evstudio.com/gypsum-association-2009-fire-resistance-manual/